Retaining Wall Blues
I swear I posted this earlier today but it never showed up... Is there some kind of approval process for new forum threads? Anyway, here goes (again):
I have a walkout basement with retaining walls on either side (big cement slabs...not stone or landscape block. They come straight out from the house and then angle outward. One of them is split at the wing and the other one is starting to (at the wing). A couple years ago or so, I had it estimated to be fixed. I think the guy said $2500 for the one and $1500 for the other, although I'm sure since the second one has become worse since then, the price has gone up.
After giving me the estimate, the man said it would be cheaper for me to have my landscaper just tear down the wings and smooth out the grade. He said it was far enough out from the house it shouldn't be a problem.
I showed it to my landscaper and he wasn't too keen on the idea. He said even if he smoothed it out there'd still be a foot high hump that would allow water to drain toward my house (bad).
I'm looking for ideas/suggestions on what to do. Do I just eventually suck it up and pay $4000 to repair the ugly retaining wall? I have a feeling that's what I'm going to have to do, but I thought I'd see if anyone had other ideas.
I think the wall is about 5 and a half feet tall at the point where it is split.
Also, I'm adding a link with pictures... let me know if it doesn't work.
Here is a link that might be useful: Retaining Wall
Comments (28)
jeanerz13
Original Author10 years agoThanks for the response. I told the guy that estimated it I didn't think there had been any rebar (I assume that's what you mean) in there. He saw a little rust colored circle and thought there had been (though we never saw anything sticking out that looked like rebar to me). I do see metal pieces at other places, but just not anything at the joint where it angles off.
The guy that estimated the work was with a foundation repair company. I don't know if they would do a whole rebuild. Do you know what kind of company I should find for that kind of thing?
I'd kind of like a nicer stone/landscape block wall there instead, but that would be insanely expensive, and I don't think you can go that high with landscape block anyway. Also, the retaining wall is joined to the house... so yeah probably wouldn't work.
I'll get some more pictures added to that link soon... at least one to show the "reinforcement" that I see in the wall... Also, another crack that isn't as big but maybe more disturbing as it is closer to the house :/
Related Professionals
Bethlehem Landscape Contractors · Arlington Landscape Contractors · Canton Landscape Contractors · Del Aire Landscape Contractors · Dixon Landscape Contractors · Fair Lawn Landscape Contractors · Hendersonville Landscape Contractors · White Bear Lake Landscape Contractors · Northlake Landscape Contractors · Adrian Decks, Patios & Outdoor Enclosures · Dearborn Decks, Patios & Outdoor Enclosures · Apple Valley Swimming Pool Builders · Burleson Swimming Pool Builders · Lincoln Swimming Pool Builders · Malden Swimming Pool Buildersjeanerz13
Original Author10 years agoOk. Added a couple pictures to the flickr set. I'll add the link again just in case...
Here is a link that might be useful: Retaining Wall
rosiew
10 years agoBumping, hoping someone who knows about wall construction will help Jean.
One thing I do know is that there are blocks that can go much higher than 5' - I see lots of them on lots where there's a big elevation change. Hopefully the cost won't be prohibitive.
Rosie
marcinde
10 years agoThese walls aren't generally contiguous with the foundation pour. They're poured afterwards and butt up against the foundation. At most they *might* be pinned into the foundation, but based on what's going on with the rest of your wall that's maybe 50-50 at best.
You probably want to start with a concrete company that does walls, slabs, and foundations. A new poured in place concrete wall is going to be your least expensive solution. Down the road if you want to make it more attractive you can have a stone veneer and cap applied easily enough.
You could do a segmental retaining wall (SRW) - the landscape blocks you referenced - but done right, that would be expensive. The way these walls work is by using geogrid at every course, extended horizontally into the earth behind the wall a distance usually equal to at least the height of the wall. That's a lot of earth work and your ac unit would need moved temporarily, etc. Also, because every SRW manufacturer makes a slightly different product, engineering fees can be 2-3x the cost of a concrete wall.
This project requires an engineered drawing no matter what is used. If a contractor tells you they don't need an engineered drawing, thank them for their time and move on.
Yardvaark
10 years agoWouldn't that be something if there was steel in the wall EXCEPT at the point where the wing begins ...!! I would not consider removing the wing and regrading. The grade is too high at those points. Fixing the gap where the wing meets the main wall does not mean that the wall is fixed for the long term, unless one knows for certain how the wall is built. It would take engineering/scientific evaluation to determine this and if the wall is fixable. If it turns out that the wall is removed and rebuilt, I'd consider reconfiguring it to take advantage of concrete's strengths instead of promoting its weaknesses. A flat straight wall is the easiest to push over. If it were curved, or faceted in a curved arrangement, the pressure of the earth would help hold it together (as gravity works in holding together a masonry building arch spanning between posts) so long as the ends of the wall were rock solid immovable. If it had batter (lean-back,) or were beefier, it would be more stable. If it were mine, I'd consider employ all of these principles in a new wall. I'd also consider reusing the existing wall material--since part of a new wall's cost would be demolishing and hauling away the old one--if it could help the overall cost. (To use this way, the old wall would need to be cut/broken up and rebuilt as stacked blocks into a thick wall with lots of batter. The appearance is as stone. It would be a portion of a new wall as you would not have enough material to do the complete job using the old wall only.)
marcinde
10 years agoWhile you're correct about the physics at play, there's nothing stopping a straight wall, built with the appropriate rebar schedule and tied into a cantilevered footing, from having a perfectly long service life (if properly designed and constructed). That's also using physics to succeed.
Depending on the design the curves could look nice, though not every design demands a curve. I just hate sinking money into walls and the cost difference between dropping in forms and pouring concrete vs having masons building up from the footer with block isn't insignificant.
Yardvaark
10 years agoAgree with you marcinde that a curve is not always called for and that a straight wall can be provide a good service life. For my own preferences, I prefer retaining walls that over overbuilt as opposed to just built enough. Even if they don't fail to the letter of the law, many built to specs later show signs of wishing they were stronger. In this case, I can see how a curved wall would add useful space and light to the below-deck area, instead of having it in the side yards ... where it look like no one cares or needs it. I could easily see the wall being built of two different materials/methods ... one intensely strong for the steep portion and a less intense wall for the lower elevation change. I like the idea of retaining walls that are to some degree "overbuilt" as they don't fail, so incorporating all the strength-building devices doesn't hurt.
jeanerz13
Original Author10 years agoThanks so much for all the replies!
Yardvaark -- I'm wondering if doing a stacked wall using the old wall would save any money since I would have to pay someone to cut up the old wall into stacking blocks and I imagine there is more labor involved with stacking a wall as opposed to just pouring it. I do think a stacked wall would look nicer though. I had a few questions about the curved idea. It looks like the walls come out to the sides some before curving... would this mean the air conditioner needs to move permanently? I expect it would have to move regardless during construction, but if it needs to be moved permanently, I'm wondering if I would have to get another entry point put in the house to hook it up... Or maybe just a longer hose? (I have no idea how these things are set up / hook up to the house, etc so maybe that's a dumb question)
Finally, do any of the methods suggested require the deck to be removed for rebuild of the retaining wall? I really would prefer not to remove it if possible. I know nothing about deck building -- if it had to be removed, would it be possible to sort of "disassemble" it and then rebuild it or would that screw with the structural integrity too much?
jeanerz13
Original Author10 years agomarcinde -- you said "This project requires an engineered drawing no matter what is used. If a contractor tells you they don't need an engineered drawing, thank them for their time and move on."
If I have a concrete specific company do the work, would they have someone on staff who does the "engineered drawing" or would they have to higher someone else. What would they do with it once they had it? Or is the "engineered drawing" like a blueprint as opposed to just "winging it"?
I'm just trying to figure out how to evaluate possible companies. I can ask "hey are you going to get an engineered drawing for this?" and they could say "yes", but I would have no idea when they did the actual work if they had one or if it was a good one or whatever.
Yardvaark
10 years agoCan't tell from your pictures how close the AC is to the back yard face of the house. If it's too close, it may need to be moved a little or temporarily. Usually, AC is where it is because it's not distant from the furnace. Can move & be re-hooked up, but one wouldn't want to move it far.
The curved wall configuration would first lead outward from the back-yard-facing foundation wall as if it was an extension of the wall. It would begin to curve immediately with a uniform radius. In the curved-wall configuration you would not need to rebuild the deck, but would need to reconfigure steps. In one possibility, a bridge-like extension of the deck would be needed to extend to steps to the landing at top of the new retaining wall. There would probably be several options in the way the steps could be reconfigured.
You're correct in that while you get "free" material from the old wall, there is a labor cost to get it. There's more labor with stacking a wall than placing "poured" concrete. So no money-saving, but a better look. The result is a look of stone vs. freeway-style concrete construction. It's the kind of project that requires someone willing and experienced in order to get the right result. I wouldn't hesitate to get involved in something like this, but I can imagine many others would not. One would not actually cut the wall into blocks, but instead cut score lines that divide it in such a manner. Then, with lots of abusive manhandling (with machines, of course) the wall would break into blocks in the demolition process. There would be some jack-hammering for the finishing touches. Of course, one must determine that there is not re-bar in it before beginning, as that would make it impossible.
deviant-deziner
10 years agoIf you got a bid for 4 K , and it was correctly engineered , I would jump on that price in a heart beat.
In my neck of the woods it would be 10 times that amount. Seriously.
We've done a half dozen projects similar to this recently and 4 K wouldn't even cover the forming costs.As far as throwing a curve at it, if its a poured in place wall you can add an additional 15 to 25 % - due to the additional formwork required. That's why you don't see too many curved poured inplace retaining walls in a modest residential setting.
You definitely require a structural engineer. In my area you would also require a soils engineer, but I'm in California which comes with a whole bunch of addtional engineers, fees, consultants.. ya da ya da ya da.....
You can hire a structural engineer separately and a concrete contractor to do the work OR you can hire an engineering construction firm. ( We do both equally and the costs work out about the same )
Either way, the calculations will have to be submitted to the planning and building dept., + be reviewed to get your building permit.If you're in MA, NY NJ or CA you'll have to have a engineer sign off, an engineer inspection, a steel and footing inspection.
PS - you could do an engineered block wall. It's not too high for that option.
Photo: form work for a retaining wall
marcinde
10 years agoThere are a few paths to getting this done. One is to hire an engineer first. The walls will stand but engineers often don't get involved in space planning and aesthetics. The second way to do it is to hire a landscape designer. When I do a project like this I get everything close and then send it to a structural engineer. It saves the client a little money on the engineering fees and they get the space redesigned by a pro who's looking at the space holistically - not just how to hold the soil back. The third way is hire a construction company and they hire the engineer as part of their proposal. I always prefer #2, but I sort of have a dog in that fight.
As to how you know if they got the engineered drawing, unless you live in a really rural area a project like this requires a permit. In most areas you need a permit for a wall over 24" high and an engineer's stamp for anything over 60".
In terms of what an engineered drawing IS, it's essentially a set of blueprints. What the engineer does is run the calculations to determine the wall's specs based on the forces it needs to resist. What is provided to the contractor is a set of drawings that tell how deep to dig the footer, how thick it needs to be, how wide it needs to be, what size rebar to use, etc. At various points along the way the building inspector checks the work to confirm that the plans are being followed.
By applying his or her stamp to the drawings, the engineer is accepting liability for the walls. The engineer definitely has skin in the game. To touch on what Yard mentioned about overbuilding, every engineer I've worked with has covered his butt by designing in one heck of a safety factor. I designed a detached garage for which I had an engineer design a structural slab floor and I asked him just how much weight *could* bear on that slab. He smiled and said "nothing that would ever fit through a garage door."
When d-d mentioned engineered blocks it made me think of another solution. Techo-Bloc makes a block called Monumental that is flippin' MASSIVE. They need to be set in place with equipment like the mini-excavator in d-d's photo but an advantage is that they don't require significant excavation. It could save you money on dirtwork.
Oh, and as far as the A/C, we move and relocate them all the time. The consensus among the HVAC guys I work with is that you can extend the lines up to about 75 feet without a dip in efficiency, assuming the system was properly sized to begin with. Being as that you're one zone north you may want to check with a local company but I'd wager you're comparable.
Here is a link that might be useful: Monumental block
jeanerz13
Original Author10 years agod-d, the $4000 estimate was just for repairing the wings... not a full rebuild. My understanding of the "repair" was to do some kind of digging and sort of pull it back into place and then anchor it... I don't know exactly what... but it didn't sound like it would require any demolition or repouring a wall. Do you have a picture of an engineered block wall? Although, if it takes big equipment to bring in the blocks, I'm not sure they could get in through the fence (I think the gate is about 3 feet wide or so)
yardvaark -- would a non curved configuration also require the "bridge" modification to the deck? Or maybe for the staircase to at least be temporarily removed? I have a feeling a "bridge" would look a little weird. But maybe not...
marcinde -- when you do number 2, do you just draw the basic design before sending it to an engineer? Or do you do that actual work as well? I'm not sure if my landscaper would do this. He sounded a bit hesitant when I had asked him about rebuilding the wall (and that was just for the wing). I guess I could ask some other landscapers.
Although I'd really like the look of a stacked block/stone wall, I'm afraid it won't be very cost effective. Anyway, I've emailed one concrete company to ask for an estimate.
Also, I updated the pictures link again. Added a few pictures to show the location of the air conditioner as well as a picture of the deck staircase. There's a natural gas line that runs under the deck staircase. I suppose something will have to be done to get that out of the way temporarily.
Here is a link that might be useful: Retaining Wall
marcinde
10 years agoDon't ask another landscaper. Ask a landscape designer. They're not the same thing.
Yardvaark
10 years agoA curved wall configuration would require that the AC be relocated to behind the new wall. A "bridge" does not imply "covered bridge" ... it's nothing more than a section of the deck extending so that it can connect to adjacent land. What ends up looking strange is whenever one has the NEED to do something, but does not do it. Any need can be made to look good.
I meant to add ... a "landscaper" usually refers to someone who primarily does some finish grading and planting. While some "landscapers" may be capable of doing more, it is not necessarily the case. Most "landscapers" do not do much in the way of site construction.
This post was edited by Yardvaark on Tue, Jul 2, 13 at 9:40
jeanerz13
Original Author10 years agoI hope I didn't offend anyone buy saying "landscaper" instead of "landscape designer". I didn't know. The person I've referred to as my "landscaper" built my flower bed and I know he's done water features for other people. Is a landscaper the guy that does the grunt work and the landscape designer the one that draws up the plans for it? Or does the landscape designer do both the design and the physical labor?
Anyway, I wasn't thinking of a covered bridge. I was just thinking it would be weird to have this square deck with a skinny section sticking out to the side of the house... like you have to walk the plank to get to the yard. Maybe it wouldn't look as strange as I'm imagining it to.
pls8xx
10 years agoThis looks like another case of guys that build basement walls using the same construction for a yard retaining wall.
I'm in agreement with most everything said in this thread, though I'm not sure all of it applies in your case in a helpful way.
On the subject of poured walls, yardvaark is correct that curved walls are stronger. The same can be said for straight walls that have angles of 30 degrees spaced no more than 20 ft apart with adequate horizontal rebar. Both resist a tilting force with less footer width. DD is right about the big jump in cost for curved walls more than 2 ft in height and or a radius less than 40 ft.
The requirement for plan drawings and who may do them will differ widely depending on location. DD lives where you can't sneeze without a permit and I live where if it's not a building you get to do anything you want without asking anyone. It's best to know what applies in your location.
To assess the problem at hand, we must know the particulars of the wall and why it is failing. There are things we know from the text description and there is more that can be gleaned from the photos. There is much more that is needed.
What is the wall thickness? is it the same for the wall attached to the house as the thickness of the wings?
What is the distance from the house to the angle? How long is the wing?
What is the wall height at the house, at the angle, and at the wing end?
I note that you are in zone 6a which will have some ground freezing. At the foot of the wall, how deep is it from the ground elevation to the top of the footer? How far does the footer extend beyond the face of the wall? Do you know what the frost depth is for your location?
Is the part of the wall attached to the house still plumb? Put a level on it to check.
I have two more important questions, but I will have to supply a graphic for you to understand how to take the measurements.
DD is probably right about a $4k price for repair being reasonable. The fact that a local contractor thinks a repair might be possible suggests the situation be not be that bad. You didn't say whether you are looking for a DIY fix or what capacity you hold for doing projects.
Yardvaark
10 years agoI guess if one built an extension to a deck that was anything like "skinny" ... or "a plank," it would look odd. But these are the kinds of things homeowners come up with, not professional designers. Usually, we try to integrate necessities in ways that make them seem spacious, well-functioning and good looking. There are ways to do it even if you can't think of them.
Design is a thinking process. A designer thinks through, in detail, how something will work out to its ultimate conclusion. Designers don't necessarily think of HOW something will be built. They are more concerned with when it is built, how it will BE. A subcontractor (which a landscaper is) implements a designer's plans. They think of HOW something will be built, not necessarily if it's going to be a great thing when it is built. (Though they can appreciate it if they want to.) They are concerned with getting the work finished and if it turns out to be not that great when it's done, as long as they've followed the plans and done the work according to specifications, it's not their fault. It would be the designer's mistake if the finished product does not work out as intended. Architects, engineers and designers design things. Contractors and subcontractors build those things. Sometimes, a person may take on both roles, being the designer and the subcontractor. In the landscape industry, it is relatively common for small-time landscapers to take on the role, without training, of designing, too. It can be because the quality level expected by the clientele is not all that sophisticated. Or it can be that a landscaper has an affinity for design and can do a pretty decent job of it. Sometimes a person has training and experience in designing and implementing and does a great job on all counts and has no trouble pleasing a sophisticated clientele. The problem posed in this thread requires a designer's expertise as there is a lot to be determined and thought through. If the designer has useful skills other than design, that's not a drawback.
jeanerz13
Original Author10 years agopls8xx -- Wow those are a lot of questions. Thanks for your interest. I'll have to get back to you on most of them. I'm definitely not planning to do it myself. I'd rather have someone who knows what they're doing take care of it.
I'm not sure what the "footer" is, so I don't know how to measure it.there's a piece of metal I see sticking out of the ground near the end of the wing... does that have anything to do with it? If it's buried under ground, I don't know how to measure it...
I did a search for frost depth and I found a map that (if I'm reading it right) puts it around 20 inches. I'm in central Missouri.
I'll probably take a few more pictures to go along with the answers to the rest of your questions --particularly the part about the wall being plumb. There's something at the bottom of the house wall, but I wasn't sure if it was a problem or just a bad finishing job... you'll see what I mean... Oh and I'll apologize in advance, my yard needs mowed so it may look a bit like a jungle :P
Here is a link that might be useful: Frost Depth
jeanerz13
Original Author10 years agoyardvaark -- thanks for that very eloquent answer explanation :)
jeanerz13
Original Author10 years agoOkay, I only took measurements from the wall with the big split. They may not all be exact, as it's difficult to measure long distances without someone else holding the other end of the measuring tape, but here they are:
Wall thickness at the house: 7 and 5/8 "
Wall thickness at the split on the side connected to the house: 7 and 7/8"
Wall thickness at the split on the wing side: 7 and 7/8"
Wall thickness at the end of the wing: 7 and 5/8"Distance from house to the split: 147 and 1/2"
Distance from split to end of wing: 138 and 1/2"Wall height (this one was tricky, some places had dirt piled up, such as what had spilled through the split... I just measured on top of it, though the wall might go an inch or two lower)
Wall height at house: 87 and 1/2"
Wall height at split: 62"
Wall height at end of the wing: 31"It looks to me like the wall is still plumb (using a level). I do have a pretty short level and I don't know if I checked at the right spot. I just chose a spot at eye level where the wall met the siding. A few new pictures will be forthcoming :)
Update: New photos added
Here is a link that might be useful: Retaining wall
This post was edited by jeanerz13 on Tue, Jul 2, 13 at 21:04
pls8xx
10 years agoThe sad thing of this situation is that with an extra $100 of concrete and $25 of steel at original construction the wall would have never failed.
There is probably little help that this forum can provide, except to give a better understanding of how the wall failed and perhaps give some insight on what proposals local contractors suggest for a fix. Whatever is done it will be expensive and a major part of the yard is going to be torn up doing it.
While you can probably get a firm price on a complete rebuild, contractors will likely only give an estimate for a fix due to the uncertainties of what will be required. It might pay you to have a backhoe operator remove all the dirt from behind the failed part before making a decision on what is to be done and which contractor to hire for the work.
jeanerz13
Original Author10 years agoWell, the first guy has come and gone. He said it would be ballpark $10,000 to "repair it the right way" just for the one wall. It was what he called the "permanent fix". He wasn't even talking about taking the whole thing out and re-doing it all. Sounding like there would be a footing poured somewhere behind the wall and then some kind of metal plate on the existing one... and it would get pulled back... I really didn't understand it. He had another cheaper option for $3500 (still for just one wall) but it wouldn't be warranted at all (though he claimed this cheaper way should last 10 years or more). Something about excavating behind the wall and laying some new drain tile and such... and using metal straps on the front side.. I don't know. I'm going to have to call some other places for more estimates... but I am not liking the outlook. Excuse me while I go and cry now. *sigh*
Yardvaark
10 years agoWithout knowing the specs., such things like "metal straps on the front side" seem like band-aids and should be ruled out as anything but a last resort. Don't despair, but I think you would do better with hiring a knowledgeable designer (probably a structural engineer) and letting him or her lead the way to a workable solution ... rather than letting contractors do the designing for you, where each proposes a different, questionable solution ... so that you can never compare apples to apples (like shopping for mattresses!) Maybe one would meet with you for a consultation fee and explain the possibilities.
jeanerz13
Original Author10 years agoThanks Yardvaark. I suppose I'll try calling one tomorrow (probably just leave a message)
Sue Reynolds
8 years agoComing from a wife of a building official... I do not see any rebar in that retaining wall pour.. Thus ...your problem. Whoever does your corrective proceedure..make sure there is rebar and the proper mix of concrete density. Make sure they hold permits and licenses. This makes them accountable.
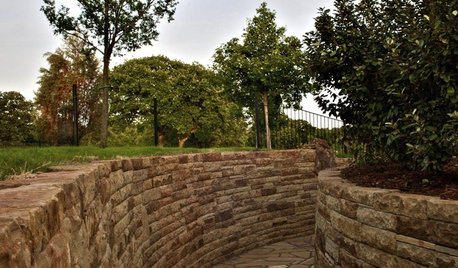
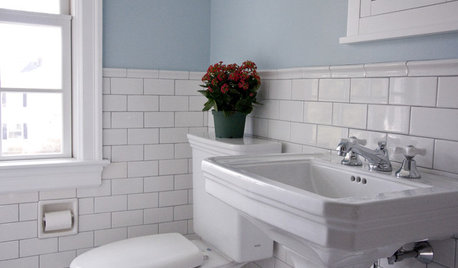
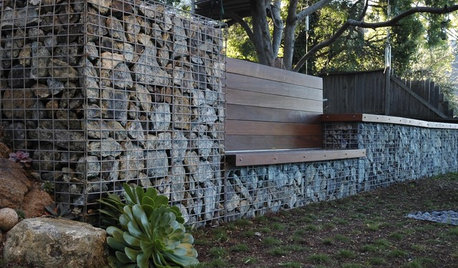
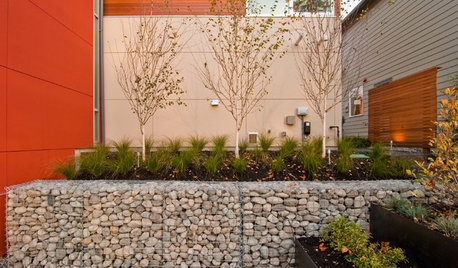
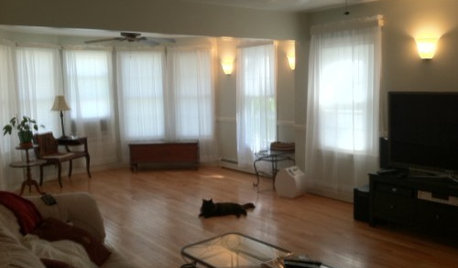
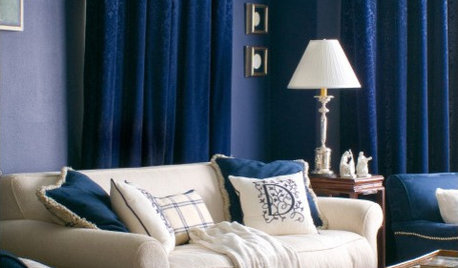
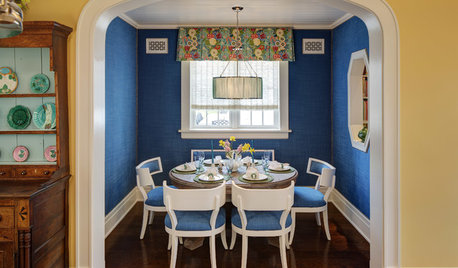
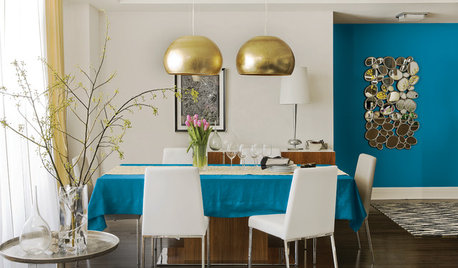
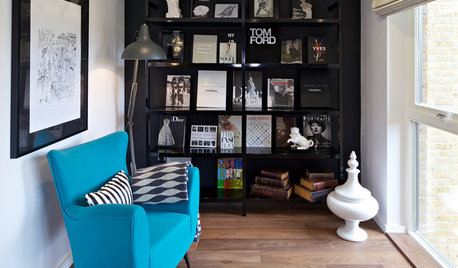
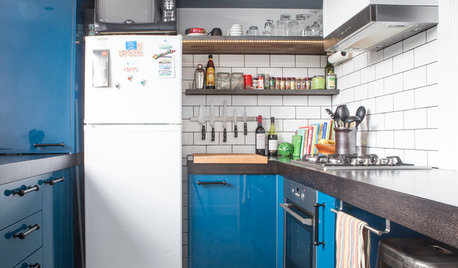
shaxhome (Frog Rock, Australia 9b)